When you can see things more clearly, you can design better solutions. In hydraulic engineering, the ability to thoroughly capture how fluids move can drastically improve our understanding of hydraulic forces and greatly enhance our ability to design smart solutions for new and reconstructed water structures.
With its 3D capabilities, computational fluid dynamics (CFD) is increasing in popularity as a method for modeling hydraulic structures. CFD offers detailed insights into complex flow behaviors — such as turbulence, free surface flows, plunging flows, hydraulic jumps and multiphase interactions — that are difficult to capture in 1D and 2D models. CFD provides a well-rounded simulation of fluid flow, considering variables such as pressure, velocity, turbulence and boundary interactions at a granular level.
CFD also includes advanced turbulence models that accurately capture small-scale flow features such as eddies, recirculation zones and flow separation. 3D hydraulic modeling can assess the entire water column, allowing engineers and designers to pinpoint potential design issues, such as areas of high velocities near the streambed, high turbulence areas at bends and cavitation from negative pressures, which cause air entrainment and uplift. CFD can accurately define precise flow patterns around intricate structures such as weirs, spillways, gates and culverts. The information CFD provides can guide design, resulting in a more stable, more efficient and longer-lasting structure.
Higher accuracy, less time
Compared to 1D and 2D models, CFD often requires more computational power and time to set up. Despite this, the improved accuracy and detailed insights it offers make it a superior tool for modeling hydraulic structures, particularly in cases in which flow complexity and design optimization are critical. Recent improvements to the cost and power of standard desktop computers, along with the expanding access to cloud computing, has helped reduce the burden of the time and computer power required to model hydraulic structures in CFD.
CFD modeling captures details such as eddies, vortices and turbulent flows that are often oversimplified or missed in 1D and 2D models. While 1D models simplify flows along a single direction (ideal for rivers or channels) and 2D models focus on horizontal flow patterns, CFD provides a true 3D analysis, giving an accurate simulation that reflects water movement and hydraulic forces. This is crucial for understanding vertical flow components and turbulence, which are common in hydraulic structures.
CFD’s detailed analysis is more reliable when designing hydraulic structures that must perform efficiently and withstand extreme conditions, such as floods. The extra detail leads to better predictions of structure performance under real-world conditions. This is especially important when engineers design sensitive features, such as pump stations and scour-critical structures. Plunging flow can be difficult to calculate, and CFD provides the assessment we need for a proper design — for instance, when we are addressing energy dissipation structures in turbulent areas. Energy dissipation calculations rely on published design guidelines developed from physical model testing in a laboratory and can be limited when applied to specific field conditions. However, by allowing site-specific analysis customized to local flow conditions, CFD leads to a design that better contains the turbulent energy and identifies downstream erosion protection needs.
This video of a CFD model shows plunging flow.
In addition to the project types mentioned above, hydraulic modelers and engineers can apply CFD modeling to help design complex storm sewer junctions, pollution dispersion, scour and sediment transport, structural rehabilitation and any project with a vertical flow component or highly complex hydraulic conditions. We’ve found 3D modeling helpful on projects involving extremely steep terrain and extensive erosion problems, energy dissipation on culvert outlets with excess velocities, drop maintenance hole designs for dam spillways, baffled energy dissipator modifications and accurate definitions of plunging flow.
CFD and public safety
Hanson has used CFD modeling to assess public safety concerns associated with low-head, run-of-river dams that are prone to the formation of hydraulic rollers. These dangerous conditions arise from recirculating currents that can trap and drown individuals, boats or debris, creating nearly inescapable hazards that can repeatedly force objects against the dam wall. Hydraulic rollers form when the downstream tailwater submerges the hydraulic jump caused by high velocity flow, pushing it toward the dam face. This is often obscured by a deceptively calm surface.
The CFD analysis provides compelling visualizations for public outreach, enhancing the awareness of these hidden dangers, and serves as a valuable scientific tool. This video showcases the CFD analysis conducted using Flow-3D software, illustrating the limited surface turbulence juxtaposed with the dangerous undercurrents. This analysis enabled a more precise determination of discharge coefficients for the ogee crest dam and helped determine the frequency of discharge and tailwater conditions that contribute to hydraulic roller formation.
The video illustrates two key conditions: the initial phase in which the tailwater depth is insufficient to stabilize a roller, allowing the log to enter the velocity jet and release downstream, and a subsequent scenario in which rising tailwater levels allow the roller to stabilize and capture the incoming log. In the latter condition, surface turbulence becomes increasingly less visible, producing a deceptively calm hydraulic condition.
The CFD analysis provides the flexibility to analyze alternative dam configurations to mitigate roller formation and enhance public safety.
This video shows a model of a hydraulic roller.
CFD and physical models
Calibration and validation are critical considerations in all phases of hydraulic modeling, and CFD is no exception. Frequently used with physical models, CFD offers a more flexible approach, enabling the evaluation of alternative structural features without the need for costly and time-consuming modifications to the physical model. A CFD analysis can often help reduce project costs by zeroing in on areas of concern while providing design assessments that better reflect true hydraulic conditions.
CFD modelers can also more efficiently alter structure designs and test new alternatives. This can help the design team find an engineering solution. By effectively informing the alternatives design process, CFD can significantly reduce the costs and time constraints typically associated with physical modeling. Hanson has recently applied this approach to the design of a pump station appurtenant with a capacity of 255 cubic feet of water per second to a 5,000-acre-foot perched impoundment for the South Florida Water Management District. Hanson conducted a CFD analysis of the pump station to develop the required structure dimensions and energy dissipation needs, evaluate drawdown in the upstream channel and determine headloss through a pump trash rack. The selected design was optimized in coordination with a physical model.
Sediment transport
CFD helps engineers analyze sediment transport and erosion patterns in hydraulic systems by providing a detailed view of how particles interact with fluid flows. The standard practice for bridge scour involves applying equations developed by the Federal Highway Administration, which were created using limited field data and laboratory experiments to determine equilibrium design scour conditions. However, one issue with this approach is the application of a single design equation to structural and river conditions that are often unique. In contrast, CFD provides sediment transport capabilities that can model complex scour conditions, such as nonuniform pier foundations and overlapping scour cones, which are often oversimplified with standard modeling procedures.
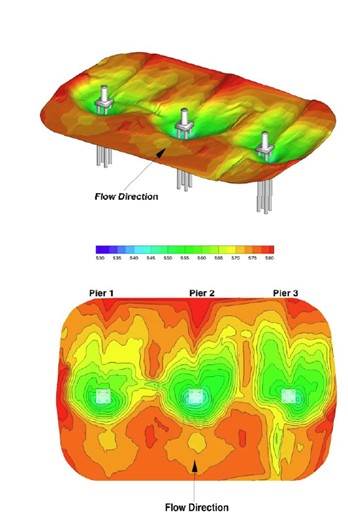
This 3D model depicts scour at bridge piers.
CFD’s ability to model 3D flow with high precision makes it an invaluable tool for modern hydraulic engineering, providing a clearer understanding of fluid behaviors around structures compared to the more simplified 1D and 2D models. To learn more about how Hanson can improve your project outcome with CFD, contact Garrett Litteken at glitteken@hanson-inc.com or Brian Wozniak at bwozniak@hanson-inc.com.