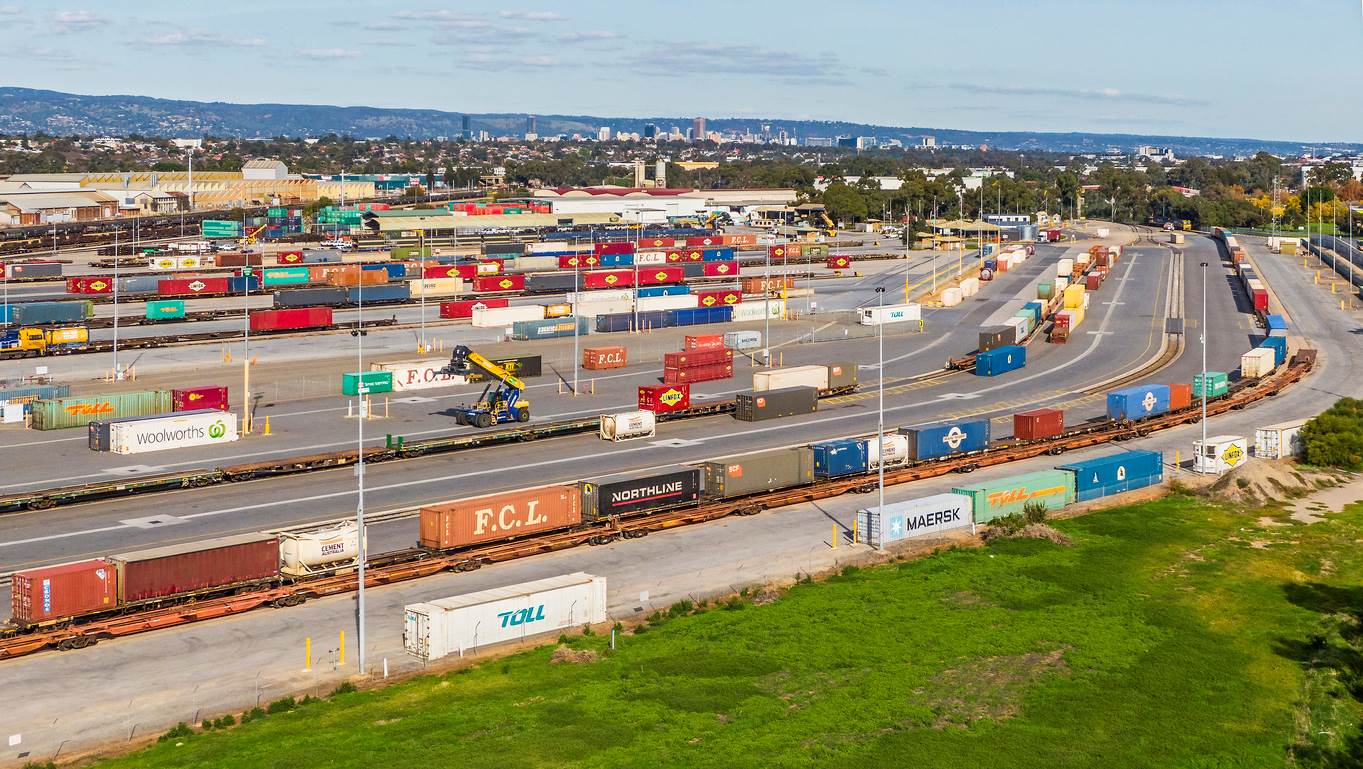
Contact Chris Bigoness at cbigoness@hanson-inc.com for a logistics evaluation of your potential site.
It’s been said that when the performance of an airplane or automobile exceeds all expectations, that machine is greater than the sum of its parts — it’s something truly special. In many ways, a rail-served industrial site is similar to a high-performance machine. If a facility’s rail operation is designed and fitted to a thoughtfully chosen site, the results can exceed expectations now and for years to come.
That’s why site selection is such a critical step in the process of creating any new manufacturing, distributing, or transloading facility. Project owners consider market reach, regional demographics, labor pool, access to transportation and utilities, tax incentives and other factors during the site selection process. This process usually produces two or three candidates. What’s the next step? Are there additional filters than can be applied to these sites to produce a clear winner?
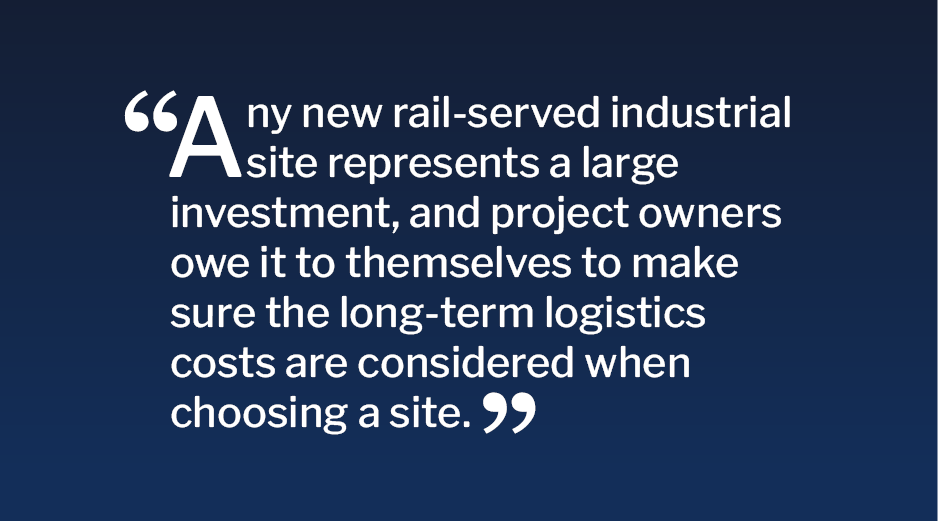
Yes — the projected annual operational expense (OpEx) of the facility. Initial capital expense (CapEx) considerations often overshadow the long-term OpEx of the facility, and this oversight can be costly, especially for a site that is intended to stay in service for 20, 30 or 50 years — or more.
This is especially true for facilities served by rail. Direct rail service ensures the capability of shippers to move high volumes of freight efficiently but comes with design requirements that differ from those of truck-only facilities. Trucks can choose many routes through a site, but rail movements are confined to one track layout. A rail layout must primarily accommodate the fluid movement of cars to and from loading and unloading areas while meeting the design requirements and service frequency of the railroad serving the facility. Some potential sites lend themselves to rail better than others.
A site rail design that uses the minimum amount of CapEx for track to get cars from a serving rail connection (or onsite storage) to the loading dock may initially satisfy production requirements, but any expansion of shipping needs or changes in railroad service frequency may quickly render the design inadequate. A costly redesign and construction may be necessary, assuming there is room on-site to accommodate additional rail infrastructure. If additional space is not available, site owners may find themselves short on options.
Our clients have found that a logistics evaluation of each site can help lead them to the right choice. Hanson rapidly performs rail suitability reviews of each site against production requirements and can offer estimated CapEx and OpEx for each site in a comparative matrix format to assist project owners with justifying an investment in an efficient and expandable rail operation.
Any new rail-served industrial site represents a large investment, and project owners owe it to themselves to make sure the long-term logistics costs are considered when choosing a site. Hanson has years of experience with industrial sites and rail operations, and a Hanson site logistics evaluation can give project owners the confidence they need to make the right decision.